倉庫レイアウトが重要な理由は?方法やポイントも紹介
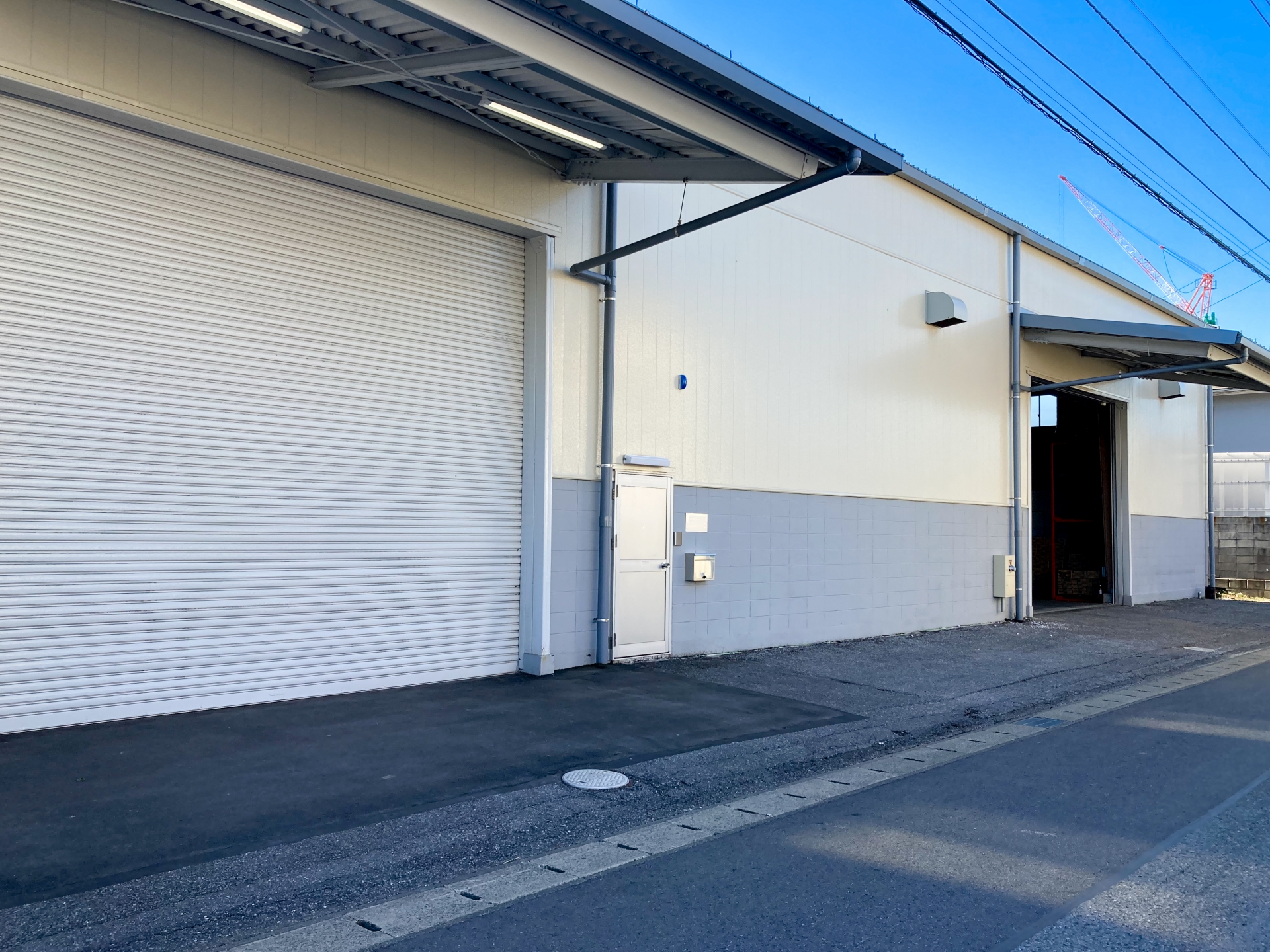
倉庫レイアウトは業務効率と安全性を大きく左右します。適切なレイアウト設計は、スムーズな作業や費用削減につながるでしょう。
ここでは、倉庫レイアウトの重要性と改善方法やポイントについてくわしく解説します。
ぜひ参考にしてください。
目次
- 倉庫のレイアウト設計が重要な理由
- 再変更が難しいため
- 作業の効率化につながるため
- コスト削減に寄与するため
- ミスを減らせるため
- 倉庫レイアウトの方法
- I字型でレイアウト
- U字型でレイアウト
- ABC分析とロケーション管理で配置決定
- 倉庫レイアウト設計時のポイント
- 作業の流れを想定する
- 倉庫の種類やスペースに合わせる
- 将来の商品や展開なども踏まえる
- 倉庫レイアウトを改善したいときは?
- 現状での課題を洗い出す
- 改善による目的を決める
- 改善にかかる時間や業務への影響を考える
- 倉庫レイアウトの注意点
- 安全性を優先する
- 収納だけにこだわらない
- 商品は出庫頻度で分類する
- 倉庫業務を改善したいときは当社にご相談ください
倉庫のレイアウト設計が重要な理由
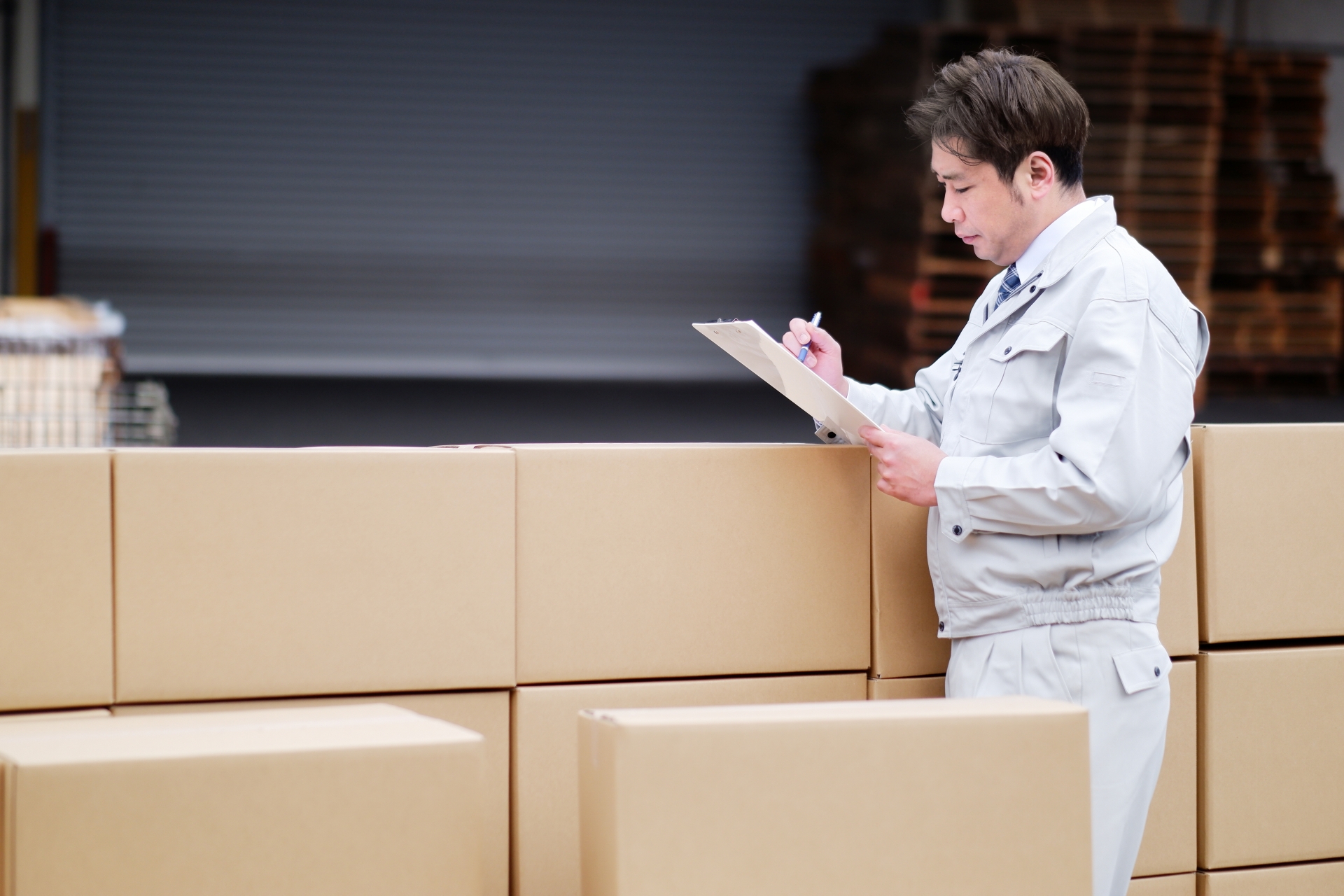
倉庫のレイアウト設計は、作業効率の最大化や安全性の向上に直結する、非常に重要なものです。効率的な運営や費用削減、事故防止のためにも、最適なレイアウトの構築が求められます。
ここでは、倉庫のレイアウト設計が重要な理由を4つのポイントから解説します。
再変更が難しいため
倉庫のレイアウトは、一度決めると頻繁な変更が難しいため、初期設計が極めて重要です。非効率なレイアウトが長期間続くと、作業効率が低下し、業務全体に悪影響を与える可能性があります。そのため現在の稼働状況だけでなく、将来の在庫予測や事業計画、さらに自動化設備の導入も考慮しながら、最適なレイアウトの設計が求められます。
慎重に設計することで、長期にわたる効率的な運用が可能です。
作業の効率化につながるため
倉庫レイアウトの最適化は、作業効率を大幅に向上させる重要な手段です。余分な移動や作業の手間を削減し、各工程での効率化を図ることで、1日の入出荷量は増え、作業スタッフの負担は軽減されます。また、不要な作業を減らすことで梱包ミスや出荷ミスなどのヒューマンエラーを防ぎ、生産性の向上が可能です。各作業スペースの内容を詳細に把握し、最適な動線を考慮してレイアウトを設計することで、商品の保管効率や作業効率を上げられます。
コスト削減に寄与するため
効率的な倉庫レイアウトの設計は、コスト削減に大きく寄与します。余分な作業や工程が減ることで出荷効率が向上し、必要な人員数を減らせます。また、余分なスペースを整理することで、倉庫レンタル費用や保管費用も削減可能です。デッドスペースの削減や作業スペースの最適化で、無駄を省き効率よく運営できるため、物流費用全体の削減が期待できます。最適化されたレイアウトは、少ないリソースによる効果的な運営に有効です。
>>物流コストとは?内訳や上がる要因、コスト削減の要点・例を解説
ミスを減らせるため
適切な倉庫レイアウトは、作業ミスや事故を未然に防ぐ重要な手段です。狭すぎる通路や見えにくい棚などの問題を解消し、十分な作業スペースや安全な動線を確保することで、人員の衝突や製品の落下などのリスクを低減します。これによって、棚卸しミスや誤発送、さらには事故による作業スタッフのけがを防ぐ可能性も高まります。業務の安全性向上や事故の予防にもつながるため、倉庫レイアウトの見直しは必須です。
>>倉庫管理・在庫管理の内容や効率化・システム化についてわかりやすく解説
倉庫レイアウトの方法
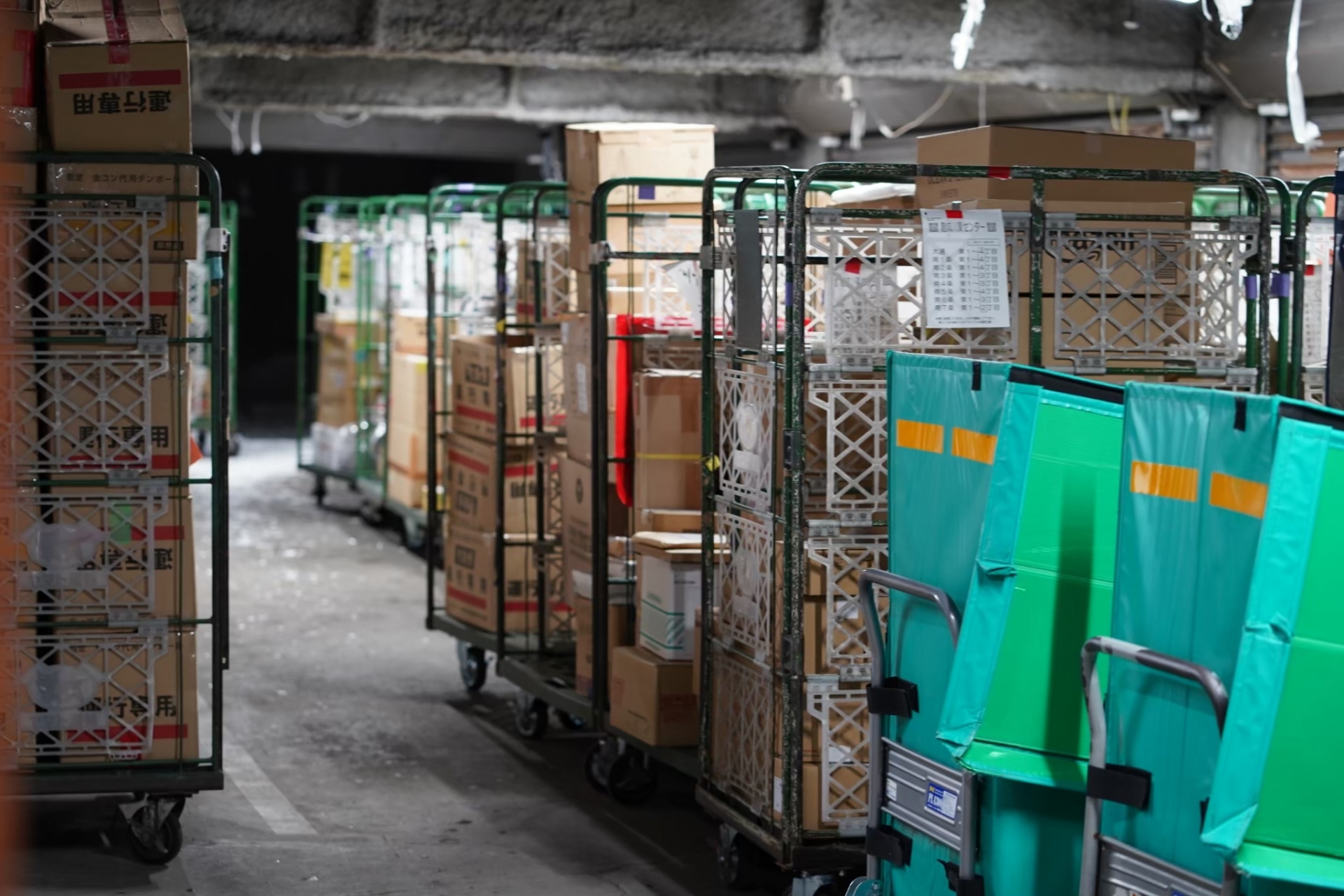
倉庫内で効率よく作業するためには、無駄を排除し、動線を最適化したレイアウトが重要です。機能性重視のレイアウトによって、余分なスペースを減らし、移動距離を短縮することで作業効率が向上し、費用削減につながります。
ここでは、効率のよい倉庫レイアウトにするための3つの方法を紹介します。
>>当社のフルフィルメントサービス(スゴロジ)の紹介はこちら
I字型でレイアウト
I型レイアウトは、倉庫内の作業フローを一直線に配置し、入荷から出荷までの流れをシンプルにする設計です。片側に入荷商品を、反対側に出荷商品を配置することで、混同を防ぐとともに効率よく作業できます。このレイアウトのメリットは、デッドスペースが少なく、狭い倉庫でもスペースを有効活用できる点です。
ただし、広い倉庫では端と端の距離が増え、作業員の移動やコミュニケーションに課題が生じます。そのため、作業スペースや移動スペースの確保が重要です。また、出荷頻度が高い商品を中央に配置することで、移動距離を短縮し、効率をさらに高められます。
U字型でレイアウト
U型レイアウトは、入荷から出荷までの流れをアルファベットの「U」の形に配置します。このレイアウトは、入荷と出荷が隣り合わせとなるため、工程が把握しやすく、改善策を練りやすいことがメリットです。また、作業スペースが狭くても対応でき、作業員同士のコミュニケーションが取りやすい点も魅力です。さらに、通路を狭めて保管スペースを拡大できるため、より効率的な倉庫運営ができます。
ただし、出荷頻度の高い商品は、適度に分散して配置する工夫が求められます。
ABC分析とロケーション管理で配置決定
倉庫内での商品管理には、ABC分析とロケーション管理が重要です。
ABC分析では、商品の出荷頻度に基づきA・B・Cの各グループに分類し、Aグループは出入り口近くに配置することでピッキング効率を向上させます。
グループをさらに5段階に細分化することで、より高い生産性を実現した例もあります。
ロケーション管理を導入して保管場所を明確にし、倉庫管理システムを活用することで作業の標準化や生産性の向上が可能です。
ロケーション管理とHTの導入によって、作業の標準化が図られ、入出庫や検品作業のミスがなくなり、在庫管理の精度がさらに向上した例もあります。
>>物流作業標準化の手法!ムダやミスを減らし効率化させる施策とは?
倉庫レイアウト設計時のポイント
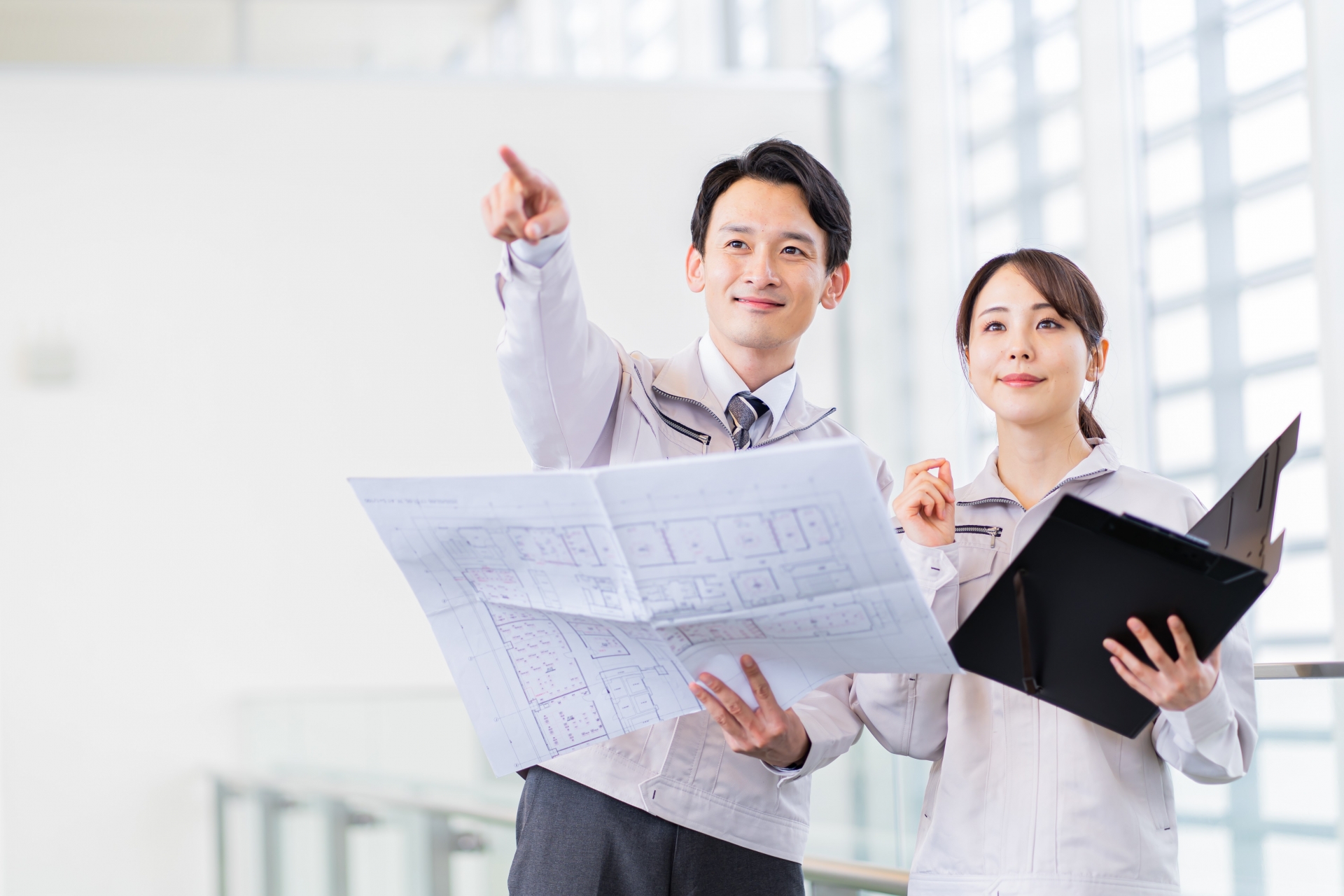
倉庫のレイアウト設計は作業効率を大きく左右する要素です。
効率のよい倉庫を運営するには、レイアウトのメリットを最大限に活かすためのポイントを押さえることが大切です。ここでは、倉庫レイアウト設計時に重要な3つのポイントを紹介します。
作業の流れを想定する
倉庫レイアウトの効率化には、入荷から出荷までの作業フローの正確な把握が重要です。具体的には、入荷・検品・棚入れ・保管・ピッキング・出荷検品・出荷の各工程を詳細に確認し、一筆書きに近い動線の設計が求められます。この方法によって、余分な移動や作業が削減され、業務のスムーズさが向上します。
業務フローを見直し、適切なレイアウトを構築することで、作業時間の短縮やミスの防止が可能です。
>>最新の物流体制を体感!当社物流センター見学の詳細はこちら
倉庫の種類やスペースに合わせる
倉庫レイアウトの設計には、倉庫の種類やスペースの特性の考慮が重要です。
在庫を多く持つと保管期間が長くなるため、商品ごとの保管方法やピッキング作業を重視します。保管スペースの拡大を優先しすぎると、作業効率が低下し、利益の減少につながる可能性があるため、作業動線や作業スペースの確保も十分に考慮する必要があります。
また、一時的な保管スペースを設けることで突発的な入出庫にも対応可能です。
倉庫の形・タイプ・床面積・取り扱う商品に応じた適切なレイアウトを設計することが大切です。
将来の商品や展開なども踏まえる
倉庫レイアウトを設計する際には、将来の商品増加や突発的な在庫対応を考慮し、空きスペースの確保が重要です。商品の一時保管や繁忙期の在庫増加に備えて、常に一定の空きスペースを設けておくことで、余分な手間や非効率を防げます。
倉庫が満杯になると、通路が塞がって作業が困難になるため、定期的なレイアウトの見直しや什器の改善も大切です。
デッドスペースを減らし、空間を活用するために適切な棚や収納を選び、将来の需要変化にも柔軟に対応できるレイアウトを心がけます。
倉庫レイアウトを改善したいときは?

倉庫レイアウトの改善には、現状の問題点を見直し、効率的な作業環境の確保が鍵です。適切な設計や必要なスペースの確保によって、業務のスムーズな運営と生産性の向上ができます。
ここでは、倉庫レイアウトを改善する際のポイントを3つ紹介します。
現状での課題を洗い出す
倉庫レイアウトを改善するには、現状の課題を詳細に洗い出すことが不可欠です。
1日の業務の流れ・作業動線・商品の保管容量・通路幅・作業員の動きを実際に観察し、さらに従業員からの現場の声をヒアリングします。課題・問題点・改善したいことを挙げて具体的に把握することで、改善策を立てられます。特にスペースロスの種類や原因を特定し、それに応じた対策を講じることで、無駄を削減し、業務全体の効率向上が可能です。
改善による目的を決める
倉庫レイアウトの改善には、発見した問題点に基づき、最終的な倉庫の目的を明確にすることが重要です。保管容量の増加・人為的ミスの削減・自動化による費用削減など、具体的な目標を設定することで、適切なレイアウト設計ができます。また、倉庫内の各業務工程を確認し、それぞれに必要なスペースを考慮したうえで、優先度をつけた改善策を講じることが求められます。特に、改善の目的に沿ったレイアウトを構築することで、効率よく成果があがる倉庫の運営が可能です。
改善にかかる時間や業務への影響を考える
倉庫レイアウトの改善には時間がかかり、その間、倉庫作業が停止または遅延する可能性があります。レイアウト変更のタイミングを慎重に決め、作業への影響を最小限に抑えることが重要です。また、レイアウトが変わることで作業内容も変わるため、従業員への教育や新しい作業手順の周知が必要です。計画段階で改善に要する時間を見積もり、その間の業務運営に支障が出ないよう、綿密な計画を立てることが求められます。
倉庫レイアウトの注意点
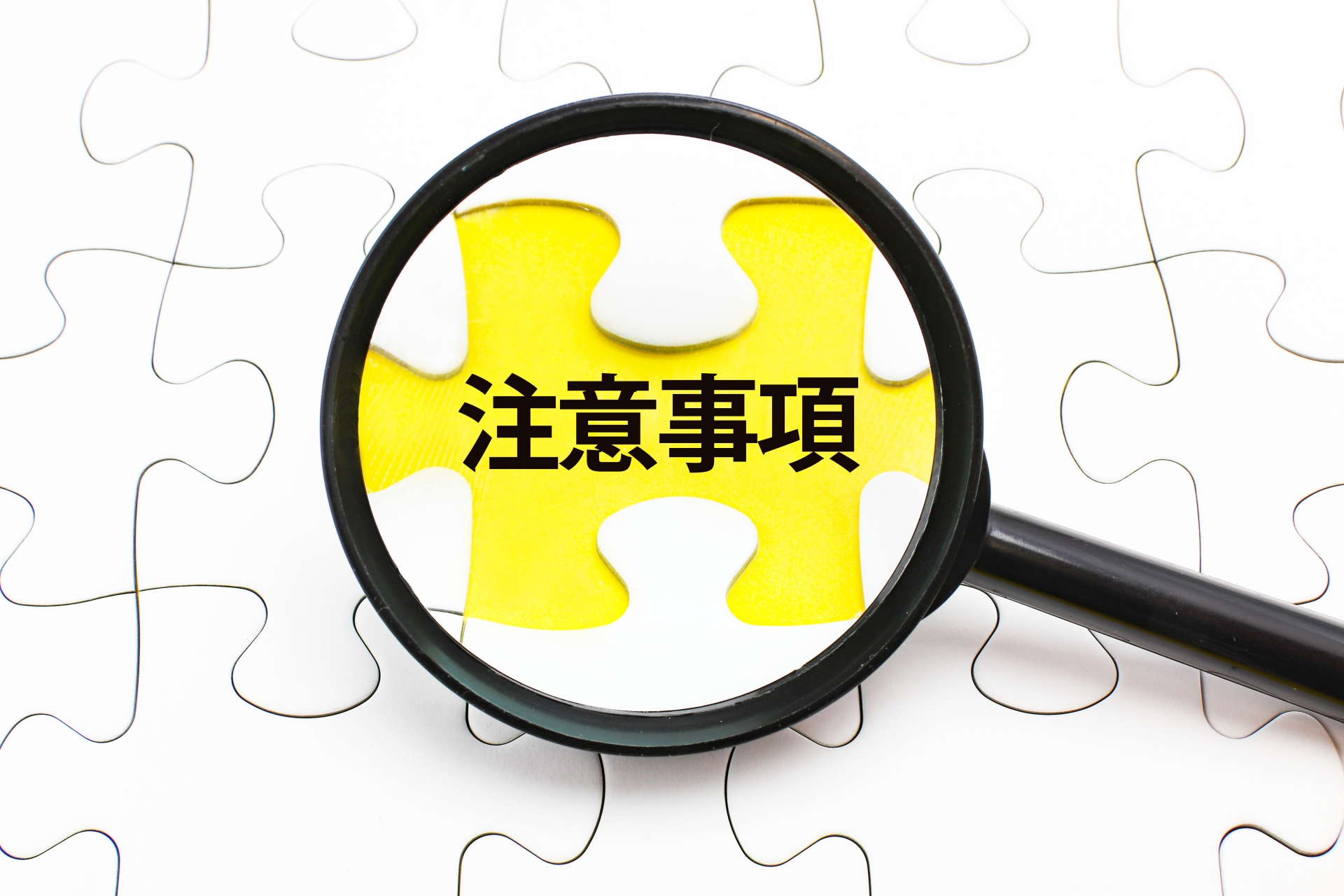
倉庫レイアウトを設計する際は、作業効率と保管効率のバランスが不可欠です。保管効率を優先しすぎると、商品が探しにくくなり、作業が非効率になる可能性があります。スムーズな入出庫を考慮した配置と適切な保管方法の検討が大切です。
ここでは、倉庫レイアウトの注意点を3つ紹介します。
安全性を優先する
倉庫レイアウトを設計する際、安全性を最優先に考えることが重要です。通路幅を広く確保し、従業員が余裕を持ってすれ違えるようにすることで、作業効率が向上し、事故のリスクが低減します。特にフォークリフトを使用する際は、十分な幅を確保しましょう。また、ラインテープを使用して保管スペースや動線を明確にすることで、誤って商品を踏んだり、ぶつかったりする事故を防げます。什器の固定や避難経路の確保、定期的な安全点検の実施が不可欠です。
収納だけにこだわらない
倉庫レイアウト設計では、収納効率や見た目の整然さにこだわりすぎると、作業効率や保管効率が低下する恐れがあります。商品の出し入れがしにくくなったり、棚の確認に時間がかかったりすることで在庫管理が難しくなる可能性があります。保管効率を高めるためには、余分なスペースをなくし、倉庫の立体的な活用が重要です。
また、収納が美しく整っていても、作業がしにくい環境では商品の取り扱いミスや品質低下のリスクが増えます。保管と作業効率のバランスを意識した実用的なレイアウトが求められます。
商品は出庫頻度で分類する
倉庫の保管効率を重視する一方で、作業効率を損なわないことも重要です。保管スペースが足りないときに、出荷頻度を無視して空いた場所に商品を置くと、作業効率が低下し、業務が滞る可能性があります。
出荷頻度の高い商品を取り出しやすい場所に配置し、出庫頻度に応じて3〜5つに分類して収納場所を決めることで、最短の移動距離で作業し効率化を図れます。見た目や種類ではなく、出庫頻度を基にしたレイアウト設計がスムーズな作業を実現するでしょう。
倉庫業務を改善したいときは当社にご相談ください
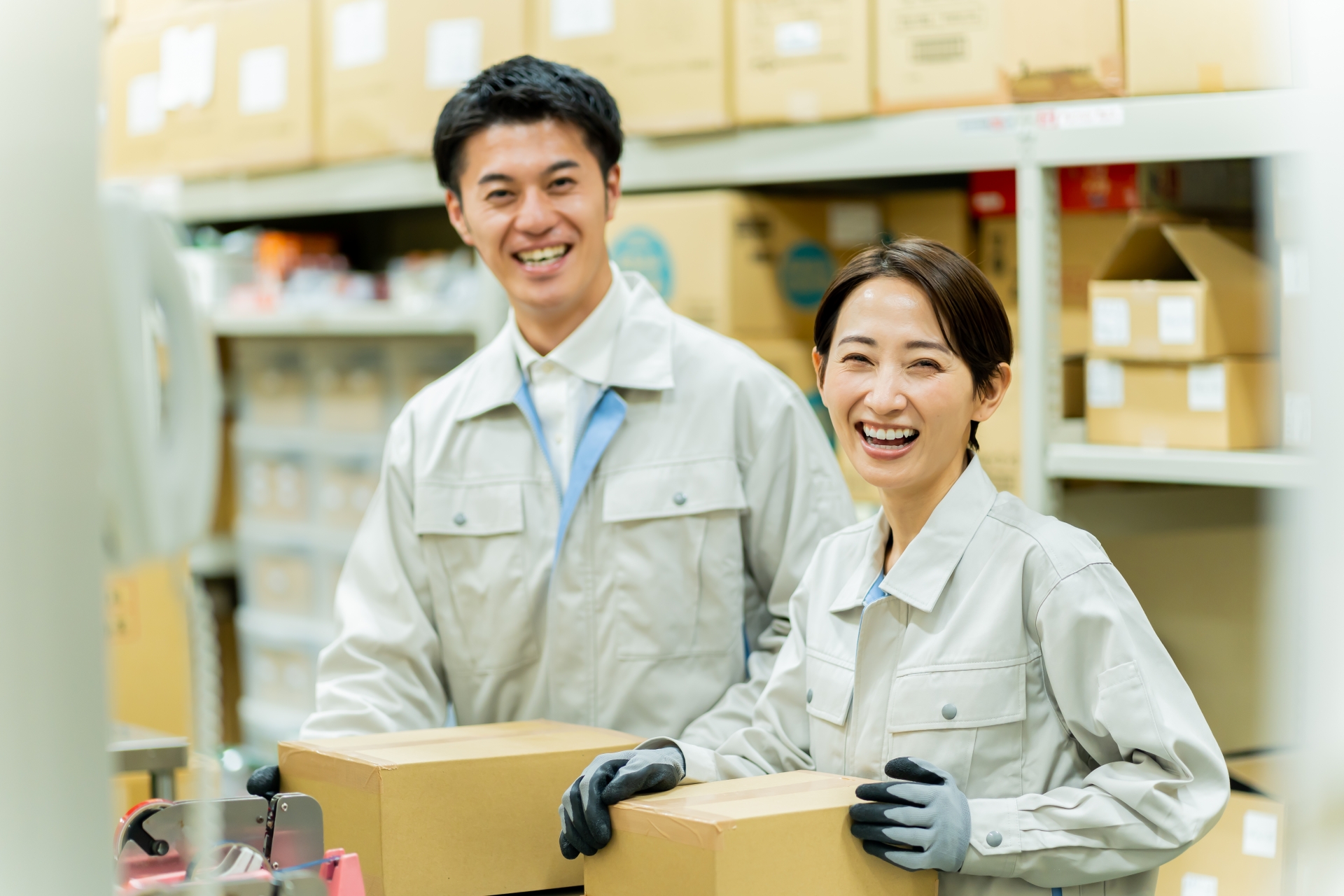
倉庫レイアウトの改善は、作業効率の向上・費用削減・リードタイム短縮・安全性の向上に大きく寄与します。ABC分析やロケーション管理を考慮した最適な動線設計が、庫内業務の効率化を実現します。
企業ごとに最適なレイアウトは異なるため、プロの物流コンサルティングや倉庫保管サービス利用の検討も有効です。
フルフィルメントセンターでは、注文受付から在庫管理・梱包・発送までをワンストップで対応し、業務の効率化と費用削減を実現します。現場での作業プロセスをごらんいただける見学を随時受付ています。
詳細や見学申し込みは下記バナーからご確認ください。